Main navigation
Specially designed for you, this tool will help you estimate, step by step, the thickness of the coating to apply and the quantity fo wire to use in all your projects, whichever corrosion classes you work with and the type of wire selected.
* The figure given above is purely theoretical and is given for information only. It therefore does not engage Zinacor S.A. in any way. In practice, you will have to take into account many technical, design and human factors that will increase the quantity to be used.
Get in touch helps us to understand you better
Rue de Chênée 53 (entrée B)
B-4031 Angleur- Belgique
Telephone +3243666471
Get in touch helps us to understand you better
Design of the parts to be metallised
Several points have to be considered.
Is metallising possible?
- Easy, safe access.
- Minimum metallising distance to be complied with.
- Dead angles to be avoided.
For more details: accessibility
Will the design make corrosion easier/more difficult?
- Presence of slots/openings between two elements.
- Avoid places where water and dirt can stagnate.
- Lifting aids to prevent coating from being damaged.
For more details: favourable/unfavourable design
Welds and edges?
- Uninterrupted welds.
- Round edges.
- Grind the laser cut parts to create a certain roughness and remove burrs, if appropriate.
For more details: welds and edges
Surface preparation
Surface preparation has a considerable influence on the quality of a coating and especially on its adhesion. Several elements are thus to be considered:
- degreasing: oil, grease, oxide and other dirt have to be removed;
- blasting:
- the surface to undergo blasting must be safely accessible,
- blast the entire surface using compressed air, including weld beads, if any,
- monitor atmospheric conditions during blasting,
- after blasting, do not touch the surface with your bare hand,
- metallising work has to be started as soon as possible after blasting,
- degree of cleanliness: the degree of cleanliness to be reached as per the ISO 2063 standard is Sa 2.50 for zinc and zinc-aluminium, Sa 3 for aluminium;
- degree of roughness: the surface roughness to be reached as per the ISO 2063 standard is Rz 50 µm to 100 µm.
For more details: surface preparation
Parameters of a metallising process
A certain number of parameters influence a metallising process:
- current: it determines the wire advance speed. The melting rate depends on the current intensity;
- voltage: voltage is an independent parameter which can be separately set. Voltage determines the thermal energy. The higher the voltage, the higher the flame temperature. Particles will hence be warmer, and thus have improved adhesion;
- pressure of the gas atomisation: pressure has an influence on the coating structure. The higher the pressure, the smaller the sprayed particles and the finer the coating structure. Compressed air thus also has an influence on the porosity and the adhesion of the zinc coating, and on the roughness of paint layers;
- metallising distance: depending upon the process (gas or electric arc), the ideal distance is between 80 and 180mm. Below 80mm, the coat may be too thick and thus lead to poor adhesion. On the other hand, above 180mm, the sprayed particles cool down before reaching the substrate, which increases the quantity of residues;
- spraying angle: the optimum spraying angle is between 80 and 90°. These data are guaranteed only in automated spraying;
- atmospheric conditions:
- substrate temperature: 3°C above the dew point,
- relative humidity: < 85%,
- room temperature: > 5°C.
For more details: metallising parameters
Quality control
Quality control must be carried out before, during and after metallising.
- visual inspection: the metal coat has to have a regular appearance, free of imperfections, without untreated surfaces, without non-sticking particles and without damage;
- thickness inspection: coating has to achieve the thickness recommended in the technical specifications, without excessively exceeding it. Thus it is required to regularly inspect the thickness during and after metallising. Inspection can be carried out using magnetic induction equipment as per the ISO 2178 standard;
- adhesion control: adhesion is an important factor which is directly linked to surface preparation. Control can be carried out on samples, using mobile or stationary equipment as per the ISO 4624 standard. The standard indicates a resistance to traction of 4MPa for a non-sealed zinc and zinc-aluminium coating;
- microscopic analysis of a sample cross-section: since this is a destructive test, this examination is carried out on test plates.
For more details: quality control
Technical advices
Contact
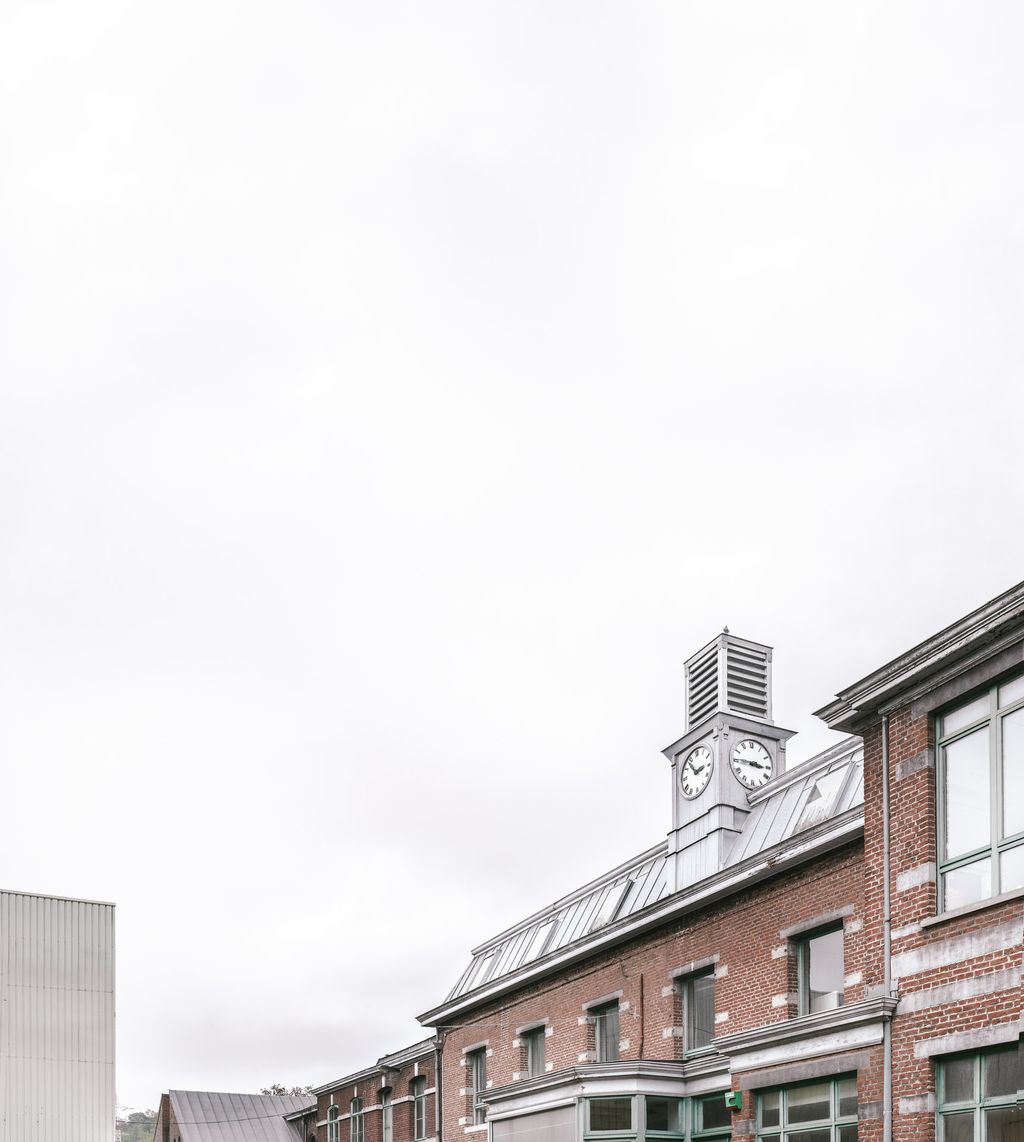
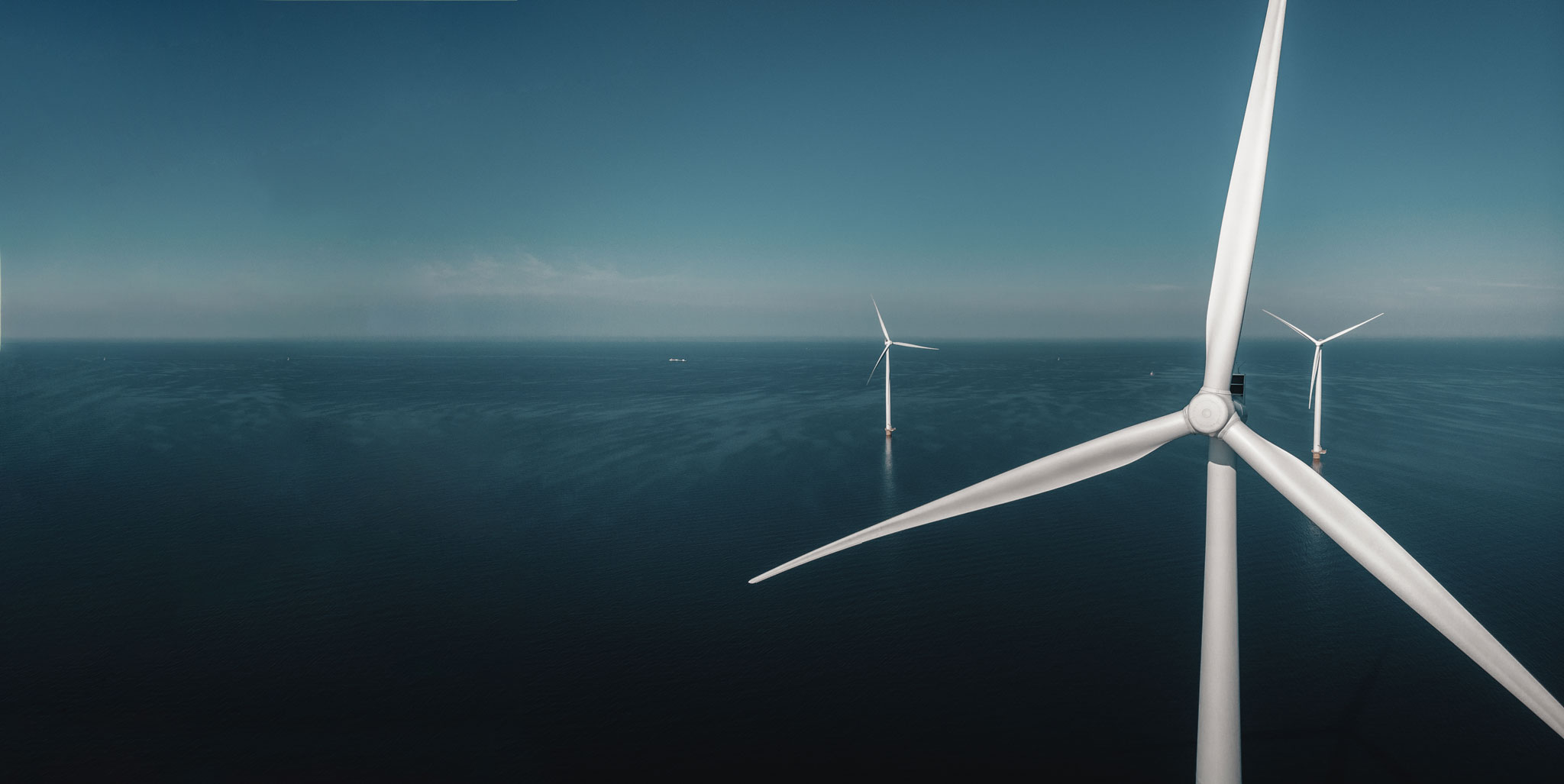
We use cookies to improve your online experience.
For more information, visit our privacy policy