Main navigation
Conçu tout spécialement pour vous, cet outil vous aidera, pas à pas, à estimer l'épaisseur du revêtement à appliquer et la quantité de fil à utiliser dans tous vos projets et ce, quelles que soient la classe de corrosion dans laquelle vous travaillez et la nature du fil sélectionné.
* Le chiffre indiqué ci-dessus est purement théorique et n'est donné qu'à titre indicatif. Il n'engage donc en rien Zinacor S.A.. Dans la pratique, il faudra tenir compte de nombreux facteurs techniques, design et humains qui vont augmenter la quantité à utiliser.
Entrer en contact nous aide bien souvent à mieux vous comprendre
Rue de Chênée 53 (entrée B)
B-4031 Angleur- Belgique
Téléphone +3243666471
Entrez en contact nous aide bien souvent à mieux vous comprendre
Design des pièces à métalliser
Il faut tenir compte de plusieurs points:
- La métallisation est-elle possible?
- accès facile et en toute sécurité
- distance de métallisation minimale à respecter
- coins morts à éviter
En savoir plus: Accessibilité
- Le design va-t-il favoriser/défavoriser la corrosion?
- présence de fentes/ouvertures entre deux éléments
- éviter des endroits où eau et saletés peuvent stagner
- aides au levage pour éviter l’endommagement du revêtement
En savoir plus: design favorable/défavorable
- Soudures et bords?
- soudures ininterrompues
- arrondir les bords
- disquer les pièces coupées au laser pour créer une certaine rugosité et enlever les bavures éventuelles
En savoir plus: soudures et bords
Préparation de surface
La préparation de surface a une grande influence sur la qualité du revêtement et en particulier sur l’adhérence. Plusieurs éléments sont donc à prendre en considération:
- Dégraissage: huile, graisse, oxydes et autres saletés doivent être enlevées.
- Grenaillage:
- il est impératif que la surface à grenailler soit accessible en toute sécurité.
- grenailler toute la surface à préparer au moyen d’air comprimé, y compris les cordons de soudure éventuels.
- surveiller les conditions atmosphériques pendant le grenaillage.
- ne plus toucher la surface à main nue après le grenaillage.
- le travail de métallisation doit commencer au plus vite après grenaillage.
- Degré de propreté: le degré de propreté à atteindre selon la norme ISO 2063 est Sa 2,50 pour le zinc et le zinc-aluminium, Sa 3 pour l’aluminium.
- Degré de rugosité: la rugosité de surface à atteindre selon la norme ISO 2063 est de Rz 50 µm à 100 µm.
En savoir plus: préparation de surface
Paramètres du processus de métallisation
Un certain nombre de paramètres influence le processus de métallisation:
- Ampérage: Il détermine la vitesse d’avancement du fil. Le taux de fusion dépend de l’ampérage.
- Voltage: Le voltage est un paramètre indépendant et peut être réglé séparément. Le voltage détermine l’énergie thermique. Plus le voltage sera élevé, plus la température de la flamme sera haute. Les particules seront donc plus chaudes ce qui améliorera l’adhérence.
- Pression du gaz d’atomisation: La pression a une influence sur la structure du revêtement. Plus la pression est haute, plus les particules projetées seront petites et plus la structure du revêtement sera fine. L’air comprimé a donc aussi une influence sur la porosité et l’adhérence du revêtement de zinc et sur la rugosité des couches de peinture .
- Distance de métallisation: En fonction du processus (gaz ou arc électrique), la distance idéale se situe entre 80 et 180 mm. En dessous de 80 mm, l’épaisseur de revêtement peut être trop importante et ainsi provoquer une mauvaise adhérence. Par contre, au dessus de 180 mm, les particules projetées refroidissent avant d’atteindre le substrat ce qui augmente la quantité de résidus.
- Angle de projection: L’angle de projection optimal se situe entre 80 et 90°. Ces données ne sont garanties que par l’utilisation d’une projection automatisée.
- Conditions atmosphériques:
- Température du substrat: 3°C au dessus du point de rosée
- Humidité relative: < 85%
- Température ambiante: > 5°C
En savoir plus: paramètres de métallisation
Contrôle de qualité
Il est impératif d’exécuter des contrôles de qualité, avant, pendant et après la métallisation.
- Contrôle visuel: le revêtement de métallisation doit avoir un aspect régulier, sans imperfections, sans surfaces non traitées, sans particules non adhérentes et sans endommagements.
- Contrôle de l’épaisseur: le revêtement doit atteindre l’épaisseur prescrite dans le cahier des charges sans pour autant la dépasser de manière excessive. Il est donc nécessaire de contrôler régulièrement l’épaisseur pendant et après la métallisation. Le contrôle peut se faire au moyen d’un équipement de mesure par induction magnétique selon la norme ISO 2178.
- Contrôle de l’adhérence: l’adhérence est un facteur important lié directement à la préparation de surface. Le contrôle peut se faire sur des échantillons au moyen d’équipements mobiles ou fixes selon la norme ISO 4624. La norme indique une résistance à la traction de 4 Mpa pour un revêtement de zinc et de zinc-aluminium, non colmaté.
- Analyse microscopique d’une section croisée d’un échantillon. S’agissant également d’un contrôle destructif, cet examen s’effectue sur des plaques de test.
- En savoir plus: contrôles de qualité
Conseils techniques
Contact
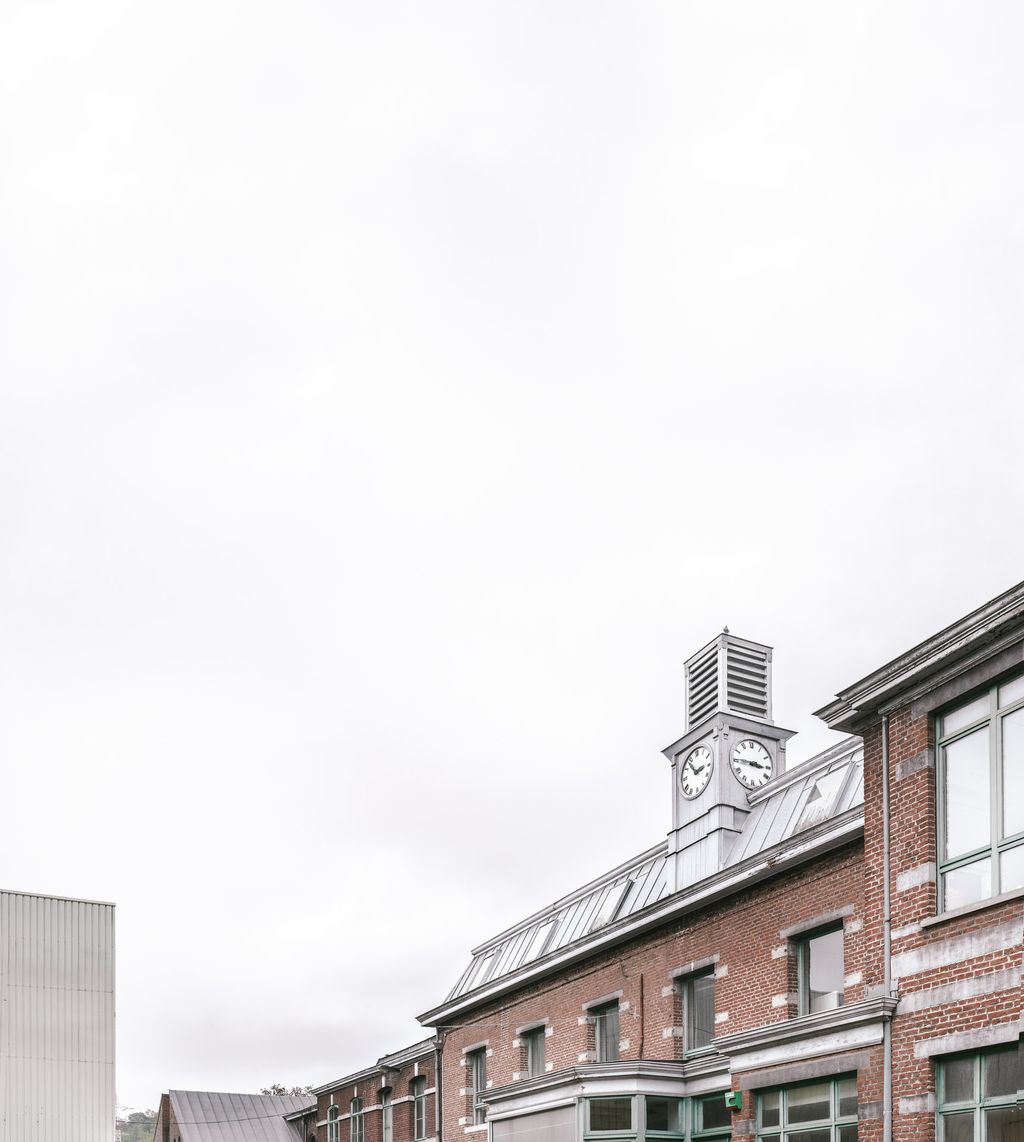
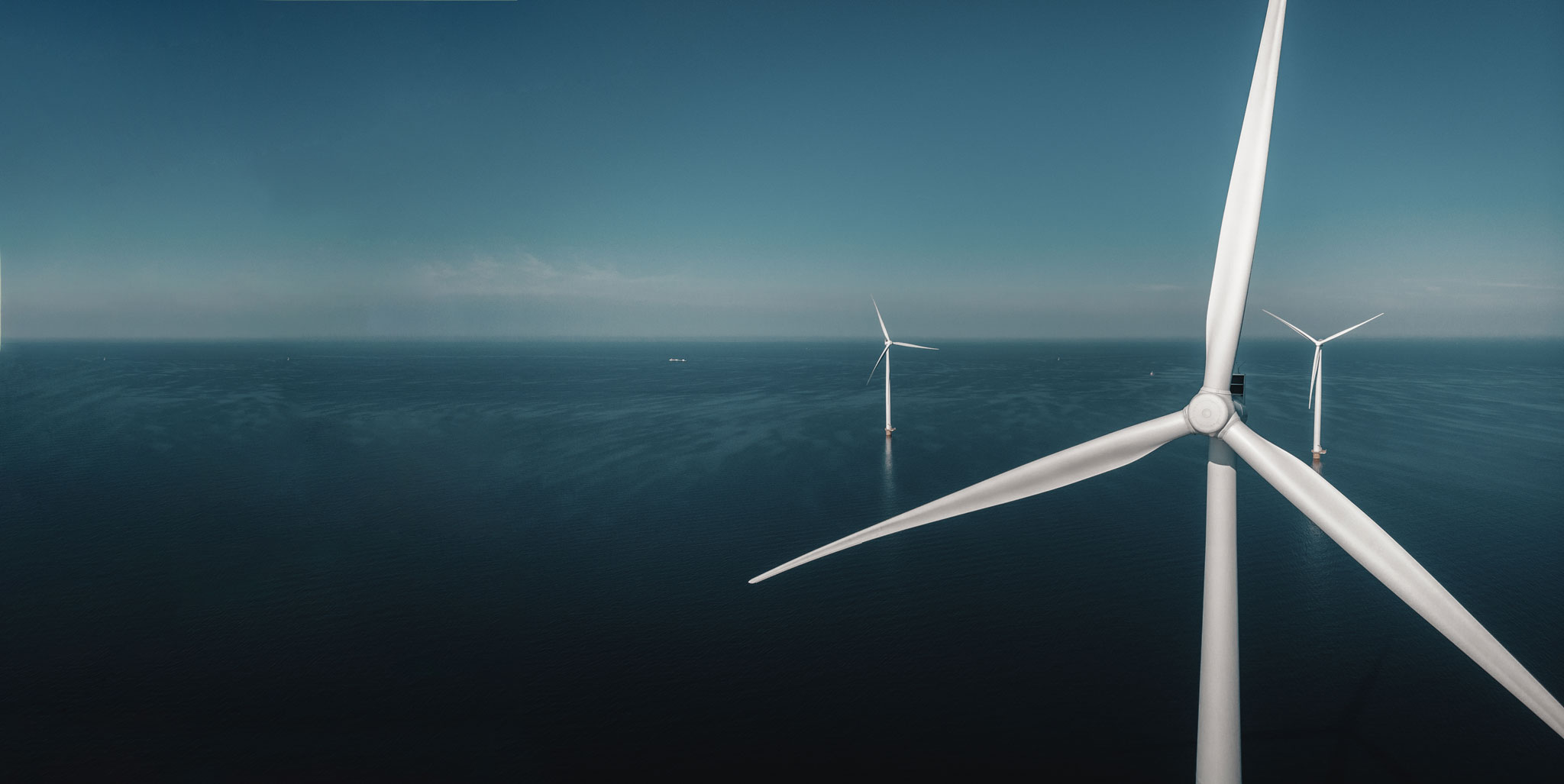
Nous utilisons des cookies pour améliorer votre expérience en ligne.
Pour plus d'information, consultez notre politique de respect de la vie privée